Filtering the Water
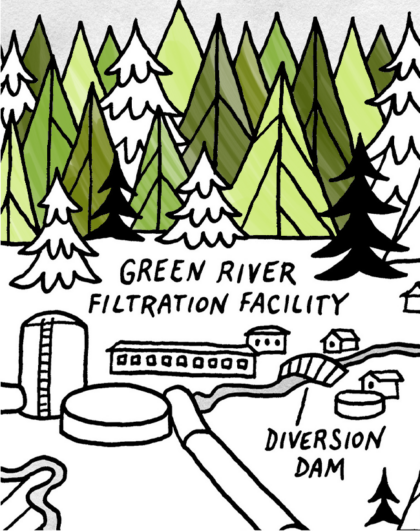
The Green River Filtration Facility brings reliability, quality, and safety to your drinking water. During filtration, the water is improved by removing contaminants and other impurities affecting taste and odor. Interested in learning more about our water system? Click the image above to download our free activity book. A great resource for adults and kids alike.
Completed in 2015, the Green River Filtration Facility is where we filter and disinfect the water we deliver to more than 300,000 people in our area.
Filtration is essential to keeping our water supply clean, safe and reliable. The process improves the water by:
- Removing pathogens such as cryptosporidium and other harmful bacteria
- Improving its taste and clarity
- Reducing the amount of silt and sand entering water pipes
- Helping reduce byproducts from the disinfection process
About the Green River Filtration Facility
Since 1913, Tacoma’s primary water supply has been the Green River. Until the Green River Filtration Facility was built in 2015, the Green River was one of the few major unfiltered surface water supplies left in the U.S.
The main reason for building the filtration facility was the need to remove cryptosporidium, a pathogen that can cause disease in humans. Though the Green River generally has low levels of cryptosporidium, we needed to meet new national standards for public health protection that called for water utilities to provide such treatment.
After thorough study and public input, the City decided that filtration was the best way to comply and keep the water safe, and so built the filtration facility at the Tacoma Water Headworks, near the town of Cumberland in south King County.
The facility continues to provide clean, healthy water, and levels of cryptosporidium remain low in the Green River water supply. We do not currently have any issues with this organism.
Watch the video below to learn more about the facility, why it was built and the processes involved in providing clean water.